Actually the steering damper makes one-handed operation way less sketchy. I'm fine with it now.
There's a much less expensive and neater aftermarket solution here.
As for the big guy upstairs I think my comfort zone to safety margin ratio is a much narrower bandwidth than most.
I thrive in the latter extremes of the B region.

Besides that I'm a pagan, a competent mechanic with highly developed motor skills and heightened perception. ...and I upgraded the brakes..

Suppose a 1000km update is a mite overdue.
It hasn't replaced my hardtail I've 2000km on that since launching the cargo. The hardtail (GT Avalanche 3.0) is just a phenomenal all-rounder it's way more fun, versatile and capable...it also fits on trains.
Both combined have replaced my car.

I've up-speced a few parts since I commissioned the craft.
Starting with the things I got wrong:
The battery placement is not the best. It makes the bike extra bouncy having 15kg of battery in the centre of the chassis. Which affects the handling considerably. I spent a week trying to relocate the batteries I have under the cargo deck to no avail. It's doable if I was to replace the batteries with a different form factor. Given I already have 4 transferable batteries I can't justify the expense of a hardmounted solution.
The compromise I made is that if I'm hauling payload then the weight distribution is normalised by the cargo and the central placement maximises cargo space so moot benefit.
If I have abundant space I relocate 2 of the largest batterys over the front wheel into the cargo area.
Having the 11kg (2kWh) at the front has considerable benefits;
The weight has a lower centre of gravity giving the bike a righting moment (below the bottom bracket) instead of a toppling one.
It keeps the front wheel down on the tarmac giving better traction thus braking effort and steering. It does a lot to keep the front wheel on the ground too on bumpy terrain enhancing handling furthermore as well as increasing the lean angle grip.
The rear tyre is as big as you can fit. If I remove it I have to true it again every time to the tyre not the rim or it will rub. I'm fine with this ( because suspension) but unless you're comfortable trueing wheels then get a narrower tyre.
I managed to shred the 11, 13, 15 & 17 tooth steel rear cassette sprockets on my first 150km fully loaded round trip with a kerb weight of ~170kg through hill country.
Mostly I can attribute this to pilot error (wrong gear uphill & starting) and lack of feedback (motor cadence too high for rider to torque sense).
You have to have mechanical empathy to operate a mid-drive correctly, it's an advanced system compared to hub-drive. I replaced the chain and cassette and used the limit screws to delete the 11T & 13T sprockets since. I now treat the 15T & 17T as downhill gears, the 20T as a level ground cruiser and the 23T as a no-brainer cruiser. Depending on the payload and hill I'll still use the 46T rear on occasion.
I haven't compromised a sprocket since.
In terms of manipulating cadence through gearing; imagine every 10mm you reduce crank arm length by being equivalent to increasing chainring size by ~2.5T.
If you do want to change the gearing a larger chainring increases top speed reducing torque and cadence as well as the increasing risk of motor stalling and FET duress .
Shorter cranks will reduce your torque but enable a faster cadence so arguably with motor assist it enables the rider to augment power at peak RPM so actually increases torque objectively.
I retrofitted a larger lighter 48T Chainring replacing the stock 46T

This improved the chainline and reduced chain dropping because it's got a phancy narrow-wide tooth profile shedding ~0.5kg being aluminium instead of steel.
After a lot of experimentation I settled on a 75mm crank arm set

The standard length is 170mm. My new cranks are a smaller radius than the chainring. It takes a bittov getting used to but you do and it's more powah = more better.
I added a set of 170mm cranks, a 15mm spanner and a crank puller to the onboard spares because there ain't a hope of moving the bike fully loaded on a hill with muscle alone with those if the motor cr@ps oot.
I'm running the same drivetrain except with 89mm cranks on my hardtail eMTB normalised to the 15T rear sprocket and this works very well.
The ideal would be a torque sensing motor...hard to find and spendy...
I've extended the chainlife by 400km on average by using a genuine KMC e-bike rated chain and splashing out on a CNC machined chain checker that compensates for roller wear.
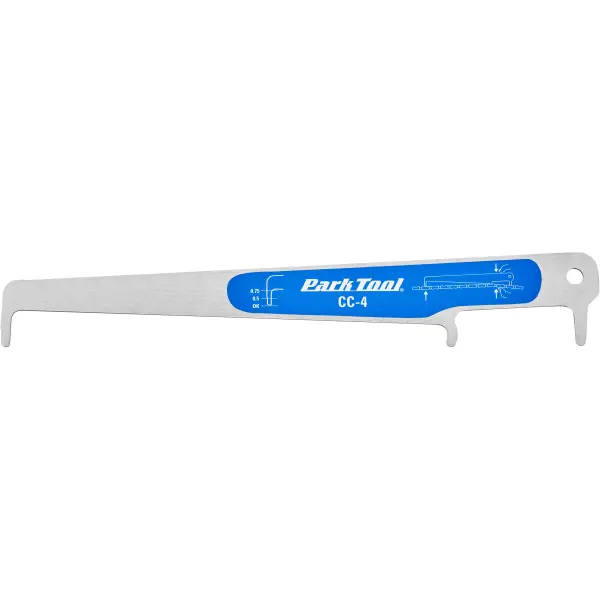
I switched lubricant to a graphite based one and chain degreaser to eco. Graphite works best for my use case being mixed terrain (road, gravel, field, hardpack, mud, stone...you name it...I'll send it
