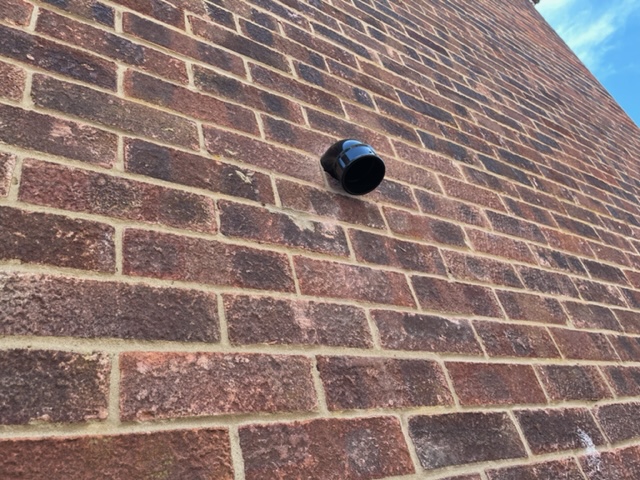
And finalised the position of the outdoor unit and screwed it down with stainless steel screws and washers.
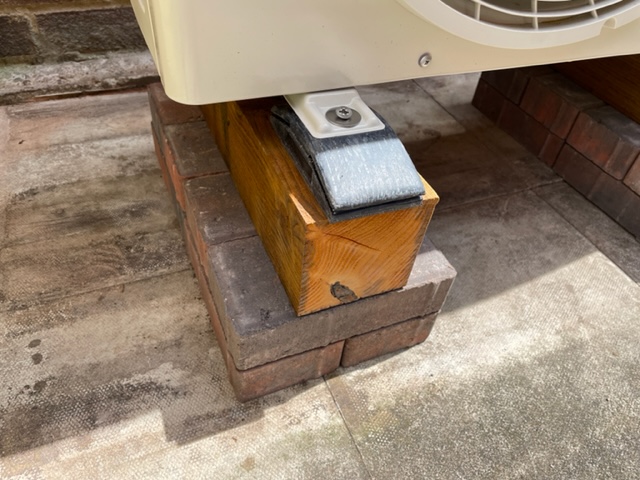
Then worked out the torque on the flared connections to the indoor unit. Different manufacture's of aircon units and flared connectors give differing values for the same size connectors.

Eventfully worked out that using a 6 inch wrench (or pushing 6 inches up the wrench), I needed to push 8kg to 11kg for the 1/4'' pipe and 18kg to 25kg on the 3/8'' pipe. Some datasheets had the torque even slightly higher so there is quite some range to be in the zone. I reckoned the 18kg to 22kg is very similar to a checked in airline flight bag with the smaller similar to a heavy hand luggage bag. The flared connections are quite different than plumbing compression fittings, in that with compressions fittings there is a lot more tightening travel, whereas once the flared connection's are hand tight, they only go another 1/4 turn and get very tight, very quickly, which actually makes them easier to do unless I have screwed them up. As you have two wrenches, its up to you whether you hold one and pull or push with the other so its very similar to lifting a similar weight like a flight bag.
Then came the pipe wrapping, the two copper pipes, the electrical interconnection and the condensation pipe. First with a plastic wrap, then with some heavy duty duct tape. I marked the point just past the connections which is the first point that the pipes can be bent once through the wall.
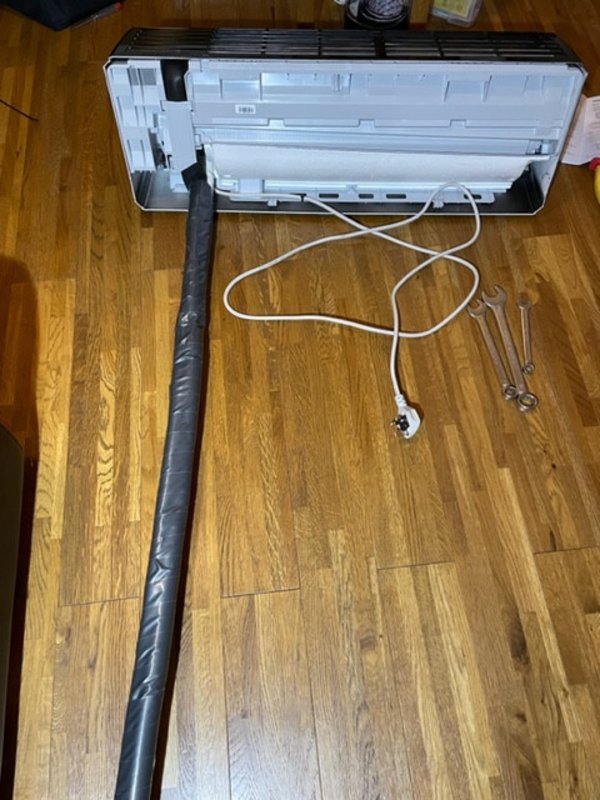